reliability
Do you have issues with the number of equipment failures you are suffering and how they affect your operations? If you don’t have confidence in your system consistently meeting operational requirements, reliability services from an independent organisation like Bamla Consultants can give you the insight and confidence you need.
Reliability Services:
- FMEA / FMECA studies
- Maintenance Strategy Optimization
- Spare Parts Strategy Optimization
- Root Cause Analysis (RCA) Studies
- Reliability Improvement
- Equipment Troubleshooting
- Equipment Optimizations
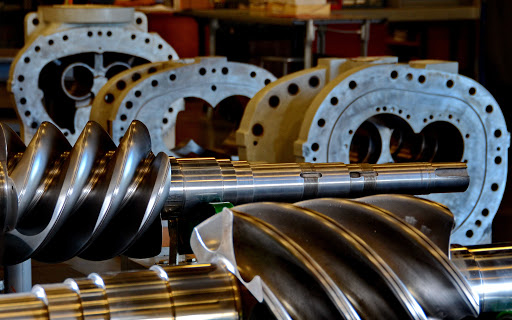
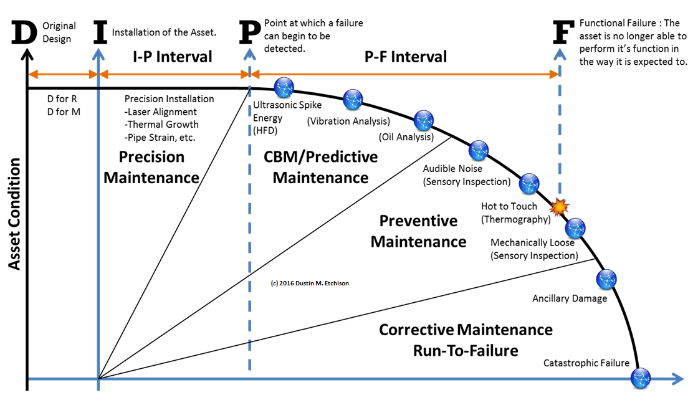
Benefits of reliability:
- Improve Availability
- Improve Reliability
- Enhance Safety
- Increase Productivity
- Reduce Maintenance Costs
- Reduce Spare Parts Costs
- Prevent Failures
Reliability of a system or a component is defined as its ability to fulfill its design functions under designated operating and environmental conditions for a specific period. The reason why Reliability Studies such as Reliability Availability Maintainability (RAM) studies must be part of every phase in the Equipment Life Cycle is that these studies can help to identify and manage asset reliability risks that could unpleasantly affect plant operations by compromising availability, performance, production and significantly increase maintenance costs. Recent studies shown that 95% of the Life Cycle Cost of an asset is determined before it is put into service. This highlights the need for Reliability Studies in the design and installation stages to identify and quantify equipment and system failures. Reliability Studies can help to identify failure modes, optimizing design requirements to enhance reliability and availability of the assets, implementing the necessary maintenance and inspection strategies to minimize the risks of failures, and consequently obtaining high availability, reliability, performance, and integrity of the assets.
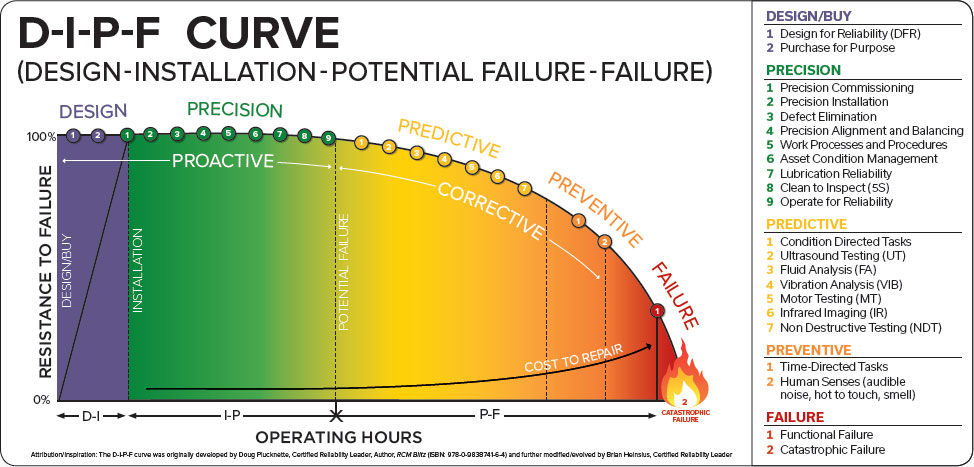
As it was mentioned before, profit is only generated during the operating phase of the life cycle. Equipment that runs without failure, at high capacity and product quality, with good efficiency and performance will produce a higher Return on Investment (ROI). To achieve this, it is necessary to have specified and selected well-designed equipment, properly installed and commissioned to high standards, operate within design limits and cared for to the standards that retain design performance. The cost of failures during operation can be reduced in one of two ways. By reducing the consequence of failure and by reducing the chance of failure. The following graphs show equipment failure rate versus time. Please note that by reducing failures and increasing availability and reliability less personnel needed on-site to carry out troubleshooting and maintaining the assets.
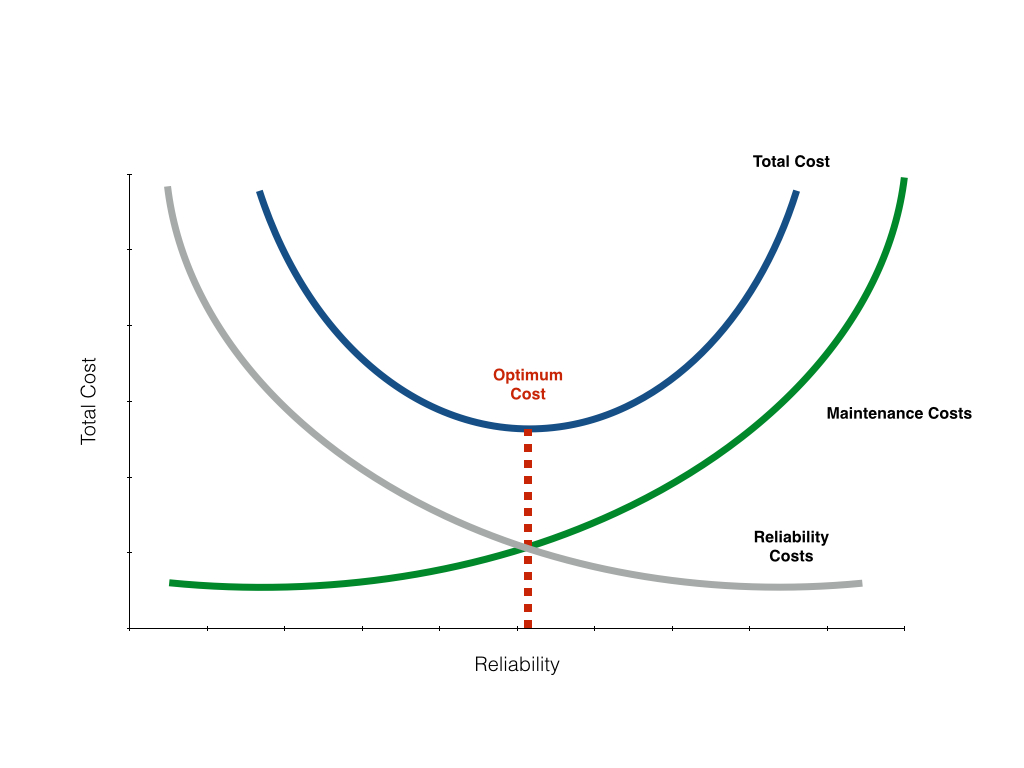
If high production and low operational cost needed, it is then necessary to create high equipment reliability by removing the causes of risk to each of the plant assets. This is where Reliability Studies such as Failure Mode Effect and Criticality Analysis (FMECA) can help to identify failure modes, reducing the consequences and probability of occurrence. FMECA is a technique used to identify, prioritize and eliminate potential failures from the system, design, or process before they occur. It is a methodology to identify and analyze all potential failure modes of the various parts of a system, the effects these failures may have on the system, and how to avoid the failures and mitigate the effects of the failures on the system. FMECA is initially performed during the conceptual and initial design phases of the system to assure that all potential failure modes have been considered and the proper provisions have been made to eliminate these failures. From FMECA studies, the engineers will be able to produce the equipment criticality list to identify operating equipment in priority order of importance, identify that equipment that can cause major costs in a case of a failure, and to select the means to prevent a failure from occurring. It is wise to know which items of the plant will cause you the greatest business-wide problems when they fail. Equipment Criticality indicates also the risk to the business. It highlights how bad a situation can become if it can occur.